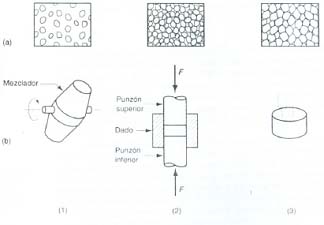
Prensado Convencional y Sinterizado
Después de la producción de polvos metálicos, la secuencia convencional de la metalurgia de polvos consiste en tres pasos: 1) combinación y mezclado de los polvos. 2) compactación, en la cual se prensan los polvos para obtener la forma deseada; y 3) sinterizado, que implica calentamiento a una temperatura por debajo del punto de fusión para provocar la unión de las partículas en estado sólido y el fortalecimiento de la parte. Estos tres pasos que algunas veces se aluden como operaciones primarias de la metalurgia de polvos se ilustran en la figura. En ocasiones también se ejecutan operaciones secundarias destinadas a mejorar la precisión dimensional, incrementar la densidad y para otros propósitos.
Para lograr buenos resultados en la compactación y el sinterizado, los polvos metálicos necesitan homogeneizarse perfectamente antes del proceso. Los términos mezclado y combinación se usan en este contexto. El mezclado se refiere a la mezcla de polvos de la misma composición química, pero posiblemente con diferentes tamaños de partícula. La combinación se refiere a la mezcla de polvos de diferente composición química. Una ventaja de esta tecnología es la oportunidad de combinar varios metales en aleaciones que sería difícil o imposible producir por otros medios. La distinción entre mezclado y combinación no siempre es precisa en la práctica industrial.
En la compactación se aplica alta presión a los polvos para darles la forma requerida. El método convencional de compactación es el prensado, en el cual punzones opuestos aprietan el polvo contenido en un dado. A la parte después de prensada se le llama compacto verde, el término verde significa que la parte no está completamente procesada. Como resultado del prensado, la densidad de la parte, llamada densidad verde, es mucho más grande que la densidad volumétrica inicial. La resistencia verde de la parte cuando es prensada es adecuada para el manejo, pero mucho menor que la que se logra después del sinterizado.
Después de prensado, el compactado verde carece de fuerza y resistencia, se desmorona fácilmente al menor esfuerzo. El sinterizado es una operación de tratamiento térmico que se ejecuta sobre el compactado para unir sus partículas metálicas, incrementando de esta manera su fuerza y resistencia. El tratamiento se lleva a cabo generalmente a temperaturas entre 0.7 y 0.9 del punto de fusión del metal [en la escala absoluta]. El término sinterizado en estado sólido o sinterizado en fase sólida se usa algunas veces para este sinterizado convencional debido a que el metal permanece sin fundir a la temperatura del tratamiento.
Las funciones de las operaciones secundarias son varias, incluyendo la densificación, el dimensionamiento, la impregnación, la infiltración, el tratamiento térmico y el acabado.
Numerosas operaciones secundarias se ejecutan para aumentar la densidad y mejorar la precisión, o para lograr formas adicionales en las partes sinterizadas. El reprensado es una operación de prensado en la cual se aprieta la parte en un dado cerrado para aumentar la densidad y mejorar las propiedades físicas.
El dimensionamiento es la compresión de una parte sinterizada para mejorar su precisión dimensional.
Impregnación es el término que se usa cuando se introduce aceite u otro fluido dentro de los poros de una parte sinterizada, Los productos más comunes de este proceso son los rodamientos impregnados con aceite, los engranes y componentes similares de maquinaria. Los rodamientos autolubricados fabricados usualmente de bronce o hierro con 10 a 30% de aceite en volumen, se usan ampliamente en la industria automotriz. Los tratamientos se realizan mediante inmersión de las partes sinterizadas en un bario de aceite caliente.
La infiltración es una operación en la cual se llenan los poros de las partes de PM con un metal fundido. El punto de fusión del metal de relleno debe ser menor que el de la parte. El proceso implica calentar el metal de relleno en contacto con el componente sinterizado de manera que la acción de capilaridad haga fluir el relleno dentro de los poros. La estructura resultante es relativamente no porosa y la parte infiltrada tiene una densidad más uniforme, así como una tenacidad y resistencia mejoradas. Una aplicación de este proceso es la infiltración con cobre de las partes de hierro sinterizado.
Los componentes de polvos metálicos pueden tratarse térmicamente y terminarse [electrodepositación o pintura] por la mayoría de las operaciones que se usan en la partes fabricadas por fundición y otros procesos de trabajo de metales. Los mismos tratamientos térmicos se usan para endurecer y hacer más resistentes las partes. Debido a la porosidad de las partes sinterizadas, se debe tener cuidado con algunos de estos tratamientos, por ejemplo, no deben usarse los baños de sales para calentar estas partes.
Se pueden aplicar a las partes sinterizadas operaciones de chapeado y recubrimiento con fines de apariencia y resistencia a la corrosión, Se debe tener cuidado para evitar que las soluciones químicas queden atrapadas en los puros, frecuentemente se usan la impregnación y la infiltración para este propósito. Los chapeados comunes para partes sinterizadas incluyen cobre, níquel, cromo, zinc y cadmio.